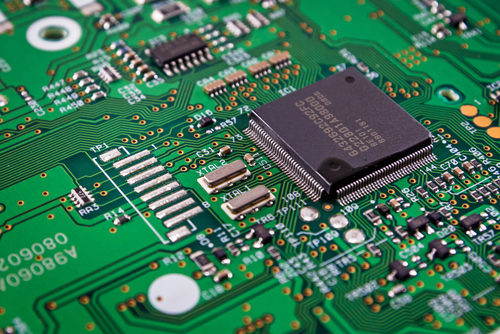
Flexible PCBs
Also known as flex circuits or flex boards, the use of flexible PCBs is growing in electronic manufacture as devices get more compact and less standard shapes are used in product design.
When to Use Flexible Circuit Boards:
Flexible circuits come into their own when it comes to manufacturing where weight and space is a major consideration. Thin and lightweight flexible circuit boards are the ideal choice when you are looking for wiring capability in spaces where the more traditional rigid boards can’t fit making them ideal for compact devices such as smart wearable’s, mobile phones and cameras.
As well as this due to their composition, flexible circuit boards have better resistance to high temperatures with a material which dissipates heat and also has resistance to shock and vibrations.
Rigid PCBs
Found in the majority of electronic manufacturing, rigid PCBs are essentially the traditional board of the world of printed circuits consisting of rigid circuitry areas. Rigid PCBs remain immensely popular, and are the solution of choice for most interconnection problems.
When to Use Flexible Circuit Boards:
Rigid PCBs are the ideal choice when cost efficiency is important, the cost to utilise only flexible PCBS being currently too expensive for the majority of production cases. Also if you are looking to develop high volumes the fabrication facility for rigid PCBs and its automation makes it the better choice unless there is a technical reason for using a flex circuit.
Similarities vs. Differences
Similarities | Differences |
|
|
The best of both worlds – Flexi-rigid PCB
A hybrid of the two, flex-rigid/rigid-flex printed circuit boards allow you to capitalise on the strengths of both board bases; keeping assembly costs down, and reliability up with the use of standard solid rigid circuit boards, whilst connecting with and utilising Flexible circuits where necessary such as in inconvenient locations, oddly shaped products and compact devices.
The use of the hybrid overall leads to a happy medium allowing electronic manufacturers to take advantage of the high functionality of flex PCBs whilst remaining cost-efficient.
Want to know about Flexible PCB production here the Newbury Group, visit our sister company Newbury Electronics’ page or alternatively contact our team today to find your solution.
Leave a Reply